Tube Production Lines
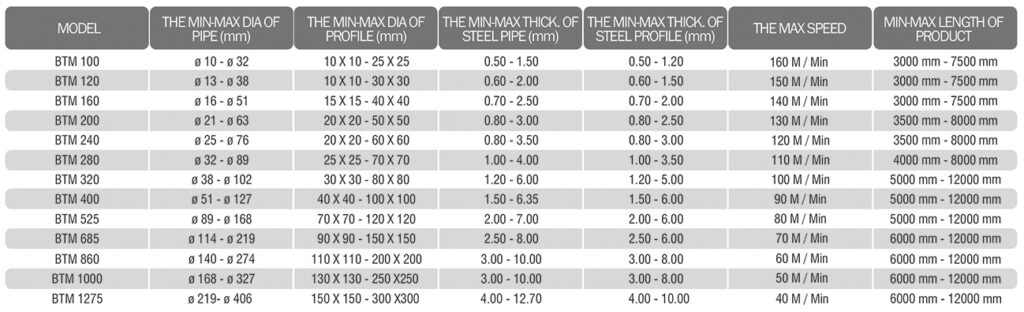
Our partner develops turnkey projects for Pipe and Section machines offering a wide range of products from Ø10 mm to Ø406 mm. Our partner taking the lead in both local and international sales take the pride in setting an example to its competitors. The following list of machines is standard, however we can produce machines in different diameter and thickness by developing customized special projects.
* The following list of machines is standard and we offer special turnkey project and manufacturing services tailored for your needs.
** The aforementioned speeds were given for ST-37 (S245) material in 6m length.
Pipe & Section Machine Consists of the Following Units:
1) Hydraulic Strip Trolley |
8) Guiding Group
9) Welding Group
10) High Frequency Welding Machine
11) Cooling Tower and Pump
12) Deburring Unit (automatic)
13) Cooling Tunnel
14) Calibration Group
15) Welding Test Unit
16) Türkankof
17) Cutting Group (cold – hot cutting)
18) Conveyor and Extractor Group (automatic)
19) Double-Sided Stacking Table
20) Driver Unit
21) Electrical Group
22) Hydraulic Group
23) All Configuration Templates
24) Replacement Part
25) Installation and Configuration
26) 1 Year Full Warranty
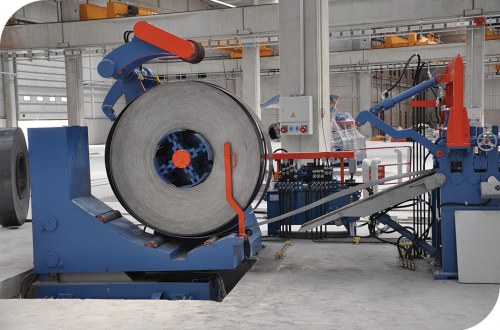
It is intended to feed the pipe machine. They are produced with double plungers or single plunger. The rotation of the double-sided ones is set automatically. Roll placement, brake configuration and top hold down roll setting are performed manually. One plunger stocks the cut roll while the other plunger is operated to decoil.
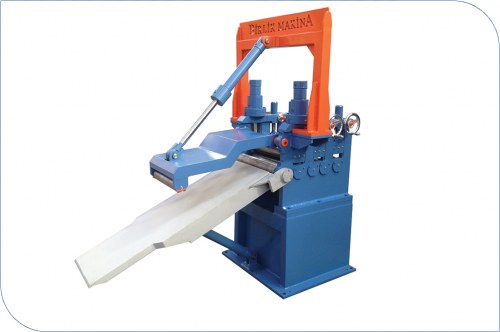
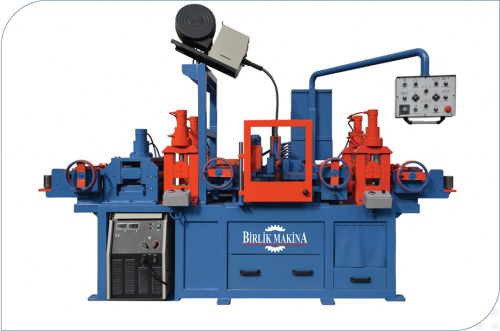
It is used to connect the ends of the strips guided after decoiler. Cutting, connecting and fixing works are performed automatically. MIG welding is used to perform the welding works.
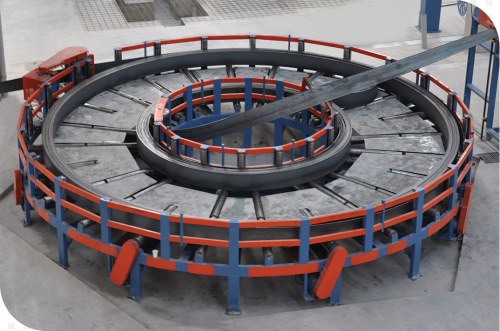
This section stocks the strips received from the decoiler in order to operate the Pipe & Section machine uninterruptedly.
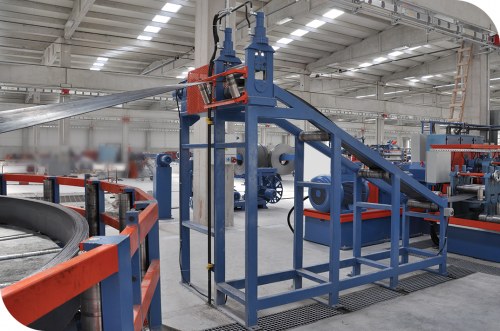
Form inlet group is used to charge the pipe machine with the strips received from spiral accumulation.
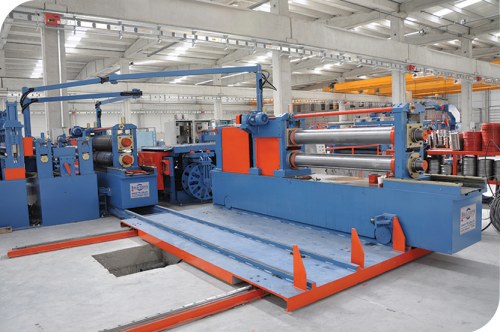
Form Group is the section where the strip is given the initial shape of the pipe. This group consists of 7 vertical stands, 7 horizontal stands, reducers, main drive motor and driveshaft.
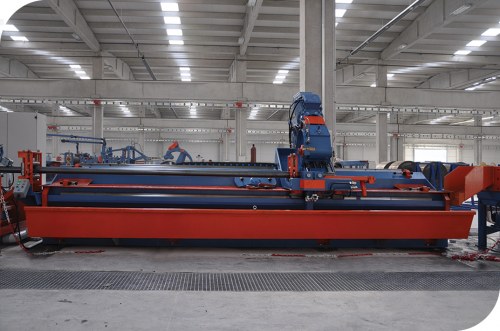
Pipes and profiles leaving Turkankof with the final shape are cut continuously in the desired lengths, and pipes are moved by a linear guide installed in the chassis and all functions are performed in parallel with the pipe machine.
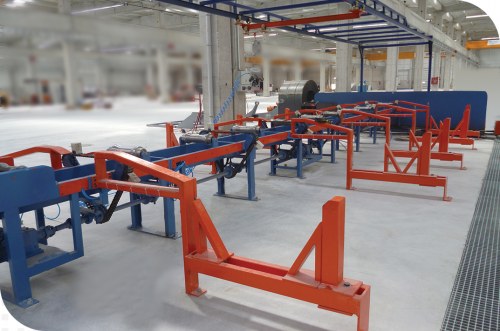